Upgrading capabilities to better serve you!
- The Purnaa Team
- Mar 29, 2019
- 3 min read
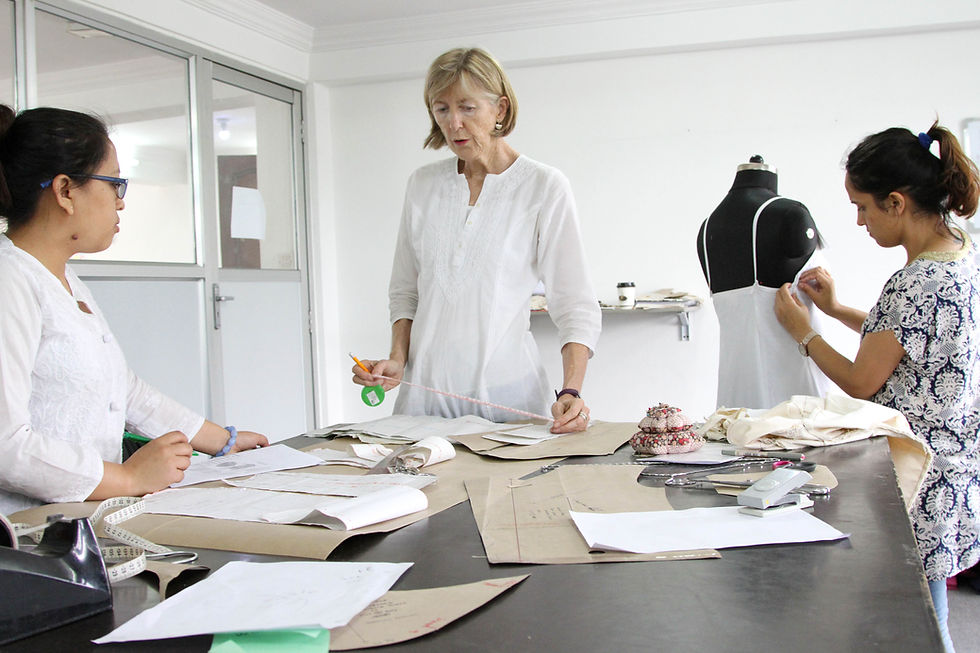
“An organisation’s ability to learn, and translate that learning into action rapidly is the ultimate competitive advantage”
– Jack Welch, former CEO of General Electric
At Purnaa we are always looking for ways to improve the contract manufacturing services we offer you, our clients. We work hard to improve systems and upskill our staff, recognizing that as we invest in their growth, we not only empower them personally but we also improve the quality of manufacturing given to our customers.
One year ago Master Trainer, Suzanne Allibone, joined the Purnaa team bringing with her 24 years of experience teaching all aspects of Garment Manufacturing for TAFE (Technical And Further Education) and formal qualifications from the Sydney Institute of Technology, Australia.
The training programs Suzanne has run at Purnaa range from 3 to 9 weeks (30-60 hours) and centre around pattern making and grading for our sample team, sewing team leaders, and intensive basic machine skills for sewers. She summarized these trainings below for those of you who are interested in topics that were covered and skills that were recently refreshed.
o 4 week (60hr) Intensive Basic Machine Skills and Basic Machine Operators training for (10) unskilled sewers on various industrial machines . Local trainers (4) were coached/mentored to run future repeat programs. All trainees were employed and successfully assimilated into Purnaa sewing teams;
o 3 week (30hr) Basic Machine Skills training refresher for Sample Team to increase skill level;
o 9 week (44hr) Pattern Making and Grading training for Sample Team. This was an introduction to international grading techniques so that our pattern makers were able to create patterns which were accurate from size to size, and shapes remained consistent with the original samples.
o 5 week (30hr) Sewing Team Leaders training which included training on Line Layout, Workstation Layout, Time study, Sewing Guides, Problem Solving, Machine Maintenance, Building Strong Teams, Quality Control, You the Trainer, and Final Assessment. Training was designed to increase understanding of new role and responsibilities, create stronger team leadership, increased initiative and activity, with a focus on identifying and solving production problems on the production floor.
Follow-up coaching is currently in place to support team leaders so we can see that they are applying what they have been taught, and to identify any learning gaps.
o Coaching Sample Team leader and weekly Sample team review. Weekly meetings with the sample team to review and improve the quality of their work on current projects, to provide alternative and more cost effective options on projects where possible, to model and develop problem solving strategies regarding pattern making and technical skills, to coach in time management, to challenge, support and encourage the team to excellence.
“So far I’ve been really happy about how things have gone”, says Suzanne, “and the feedback has been both encouraging and incredibly positive, and we’re seeing results. When working in countries such as Nepal, changing habits and transferring knowledge can be a slow process especially when education levels are so varied among the staff. Repetition is the key to growth!”
Due to the difficult environment, improvement comes slowly and learning is best done through repetition.
We are so grateful to Suzanne and the other trainers for improving our production capabilities and quality, resulting in quicker and more efficient production, reducing your costs of manufacturing. As we continue to learn and develop, our main goal is to provide the best quality and production service to our customers.
Comments