Stuffed Toy & Doll Safety Testing Requirements: What Inspections and Standards Do I Need to Follow?
- The Purnaa Team
- Feb 16, 2024
- 4 min read
Updated: Jul 8, 2024

Ensuring the safety of stuffed animals and dolls is paramount. But it’s hard to know what types of inspections are required, which safety tests to order, and what standards to follow.
From rigorous global standards to country-specific regulations, manufacturers and sellers must navigate a complex landscape of testing requirements to guarantee toy safety.
Why are testing requirements for stuffed toys so strict?
Stringent testing requirements for stuffed toys and dolls stem from the need to safeguard children from potential hazards. Young children, especially infants and toddlers, are prone to exploring the world through touch and taste, making them particularly vulnerable to the risks posed by unsafe toys.
From choking hazards to exposure to harmful chemicals, the consequences of substandard toy safety can be severe. Therefore, regulatory bodies and industry standards organizations have established comprehensive testing protocols to mitigate these risks and uphold the highest safety standards.
What are the global testing requirements for toys and dolls?
In the global marketplace, manufacturers and sellers of stuffed toys must adhere to a multitude of regulations and standards to ensure compliance with safety requirements. Organizations such as the International Organization for Standardization (ISO) and the European Committee for Standardization (CEN) have developed standards such as ISO 8124 and EN 71, respectively, which outline testing procedures for toys, including stuffed animals.
These standards cover various aspects of toy safety, including mechanical properties, flammability, and chemical composition, among others. Compliance with these standards is essential for accessing international markets and building trust with consumers worldwide.
Toy standards vary by country, so it's important to be familiar with the requirements in the region you are importing into.
What are the US standards and requirements for toys and dolls?
In the United States, the Consumer Product Safety Commission (CPSC) oversees the safety of consumer products, including toys. The CPSC has established specific regulations, such as ASTM F963, which outlines safety requirements for toys intended for use by children under 14 years old. This standard addresses various aspects of toy safety, including physical and mechanical properties, flammability, and chemical composition. Manufacturers and importers must ensure that their stuffed toys meet the requirements outlined in ASTM F963 before they can be legally sold in the US market.Â
Importers must provide a Children's Product Certificate to their distributors and retailers with each shipment. This applies to both imports and domestic products. According to CPSC regulations, an electronic certificate is considered part of the shipment if it has a unique identifier and can be accessed through a URL or other electronic means. Both the URL and unique identifier must be created in advance and available with the shipment.
Keep up to date with regulatory requirements by regularly checking in with industry resources such as the Toy Association.
Metal detecting and why it's required
Metal detection plays a crucial role in ensuring the safety of stuffed toys, particularly in preventing choking hazards. Small metal objects, such as sewing needles or wire fragments, can pose a significant risk if they are accidentally ingested by a child. Therefore, manufacturers often are required to implement metal detection systems to identify and remove any metal contaminants from their products before they reach the hands of consumers. This proactive approach helps to minimize the risk of choking incidents and demonstrates a commitment to product safety.
How do I get my products tested?
Request your manufacturer to send samples to reputable testing facilities such as SGS or TUV for inspections. The US Government's list of approved testing agencies can be reviewed here.
Set a regular schedule for periodically retesting samples as you reorder products in the future. At minimum least once per year for most manufacturers. You need to retest your production batch any time a material change has been made that could impact compliance of the product with any applicable children's product safety rule.
Questions to ask your manufacturer before producing toys
What additional systems do you have in place to ensure that toys are produced safely?
Do you have a metal detector system in place?
What quality management and inspection systems do you have in place?
Do you work with reputable testing providers?
How we manage toy safety at Purnaa
At Purnaa, we implement robust testing and quality control measures for our stuffed toys and dolls.
All our toys undergo thorough safety inspections, including metal detection, to ensure that they are free from any potential hazards.Â
We maintain a secure area dedicated to metal detection, eliminating the possibility of contamination with metal products during the manufacturing process.Â
We collaborate with reputable testing laboratories, to conduct comprehensive safety tests and inspections on our toy samples, ensuring compliance with regulatory requirements and industry standards for the country of destination.
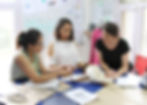
Our experienced team of project managers are ready to help you navigate the latest standards and safety testing requirements that apply to your brand. To find out how Purnaa can help manufacture your stuffed animals, toys or dolls contact sales@purnaa.com
Get Started Manufacturing
Purnaa is a full-service sewing and knitting fair-trade, social enterprise manufacturing company in Nepal with a mission to create jobs that empower marginalized people to fresh starts and fulfilled lives. We specialize in stuffed animals, toys, dolls and fully custom contract sewing and knitting manufacturing.
To learn more about how our manufacturing process works, check out these other posts: